Tümdevre üretiminde temizlik süreçleri
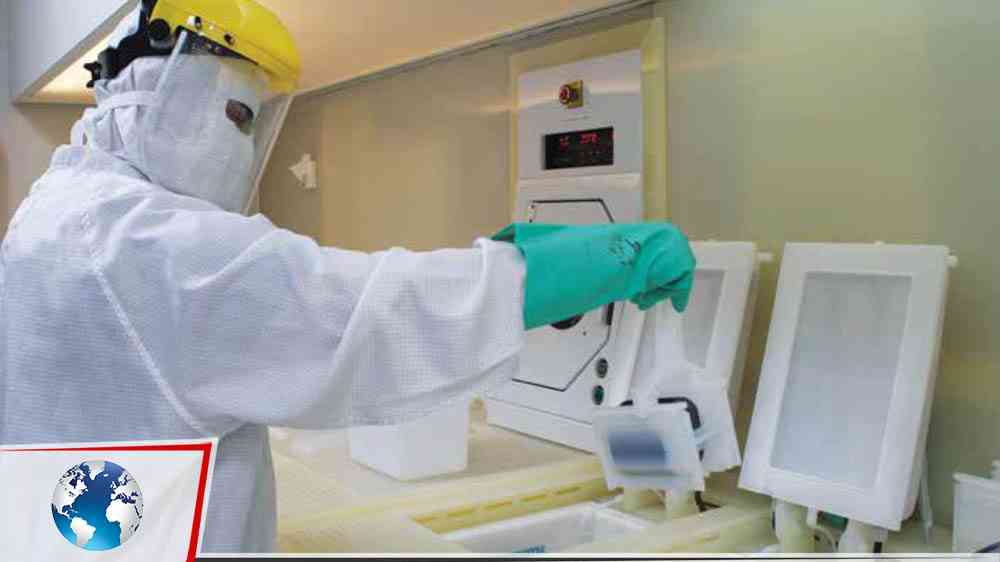
15/02/2023 16:35
15/02/2023 16:35
Yarıiletken üretimindeki en önemli süreçlerden biri, silisyum pul yüzeyinin temizlenerek sonraki işlemler için hazır hale getirilmesidir. Temel amaç, yüzeyde bulunan kontaminantları uzaklaştırmak ve yüzeyde kimyasal olarak büyüyen malzemeyi (çoğunlukla silisyum dioksit) kontrol altında tutmaktır. Pul yüzeyindeki kontaminasyonun kontrolü için teknolojiler geliştirilmeseydi, modern tümdevrelerin üretimi mümkün olmazdı.
Pul temizliği, tümdevre üretiminde en sık tekrarlanan adımdır ve dolayısıyla üretimdeki en önemli süreçlerden biridir. Tümdevre ve eleman boyutları küçüldüğünde, yeni cihaz ya da malzemeler üretim sürecine girdiğinde, kirlilik seviyesinin daha da azaltılması gerektiğinden temizleme işlemi daha karmaşık hale gelmektedir. TÜBİTAK BİLGEM’de tümdevre üretimi gerçekleştiren YİTAL laboratuvarında 0.25 µm devre üretimi kapsamındaki toplam yaklaşık üç yüz adımdan altmışı temizlik süreçleridir.
Kural olarak, kirletici parçacık boyutu transistör hat genişliğinin yarısından daha küçük olmalıdır. Yani, 250 nm teknolojisi için 125 nm’den daha küçük boyuttaki, 180 nm teknolojisi içinse 90 nm’den daha küçük boyuttaki partiküller uzaklaştırılmalıdır. Küçük partikülleri uzaklaştırmak daha zordur çünkü daha fazla enerji gerektirmektedir. Temel olarak 4 farklı kontaminasyon tipi ve kaynağı bulunmaktadır;
√ Partikül: Ortamdaki toz, polen, giysi, bakteri vb. kirlenmeye neden olabilir. Çapı 20 mikron üzeri olan parçacıklar yere çökse de 0.1-20 mikron büyüklüğündeki parçacıklar tümdevreleri kirletebilmektedir.
√ İnorganik maddeler: Tuzlar, çözelti içindeki pozitif-negatif iyonlar, ağır metal atomları inorganik kontaminasyon oluşturan malzemelere örnektir. Bu tip kontaminantlar, özel çözeltiler veya su yardımıyla pul yüzeyinden uzaklaştırılır.
√ Organik maddeler: İs/duman, deri döküntüleri, yağlayıcılar, solvent buharı, borulardan gelen monomerler, organik kontaminant organik kirlenme oluşturabilmektedir. Bu kontaminantlar da gaz veya sıvı fazda oksitleyiciler ile giderilmektedir.
√ Safsızlıklar: Pul yüzeyindeki safsızlıklar, katman depolama veya ısıl oksidasyon süreçleri sırasında süreç gazlarından gelen maddelerdir veya yüzeyde biriken reaksiyon artıklarıdır. Bu safsızlıklar katı veya sıvı süreçler ile giderilmektedir ancak yüzeyden uzaklaştırılamadığı durumlar da mevcuttur.
YİTAL’de temizlik işlemleri çoğunlukla katman depolama ve ısıl oksidasyon süreçleri öncesinde gerçekleştirilmektedir. Sağlıklı depolama ve oksidasyon işlemlerinin gerçekleştirilebilmesi için pul yüzeyinin temiz olması gerekmektedir. Pulun temiz olması üretim araçlarının da temiz kalması açısından önemlidir. Bunun yanında üretim sırasındaki bazı adımlardan sonra da reaksiyon artıklarını uzaklaştırmak için yine temizlik işlemleri yapılmaktadır.
Tümdevre Temizliği Nasıl Yapılır?
YİTAL’de, genellikle sıvı-faz temizlik yöntemleri kullanılmaktadır. Başlıca kullanılan kimyasallar ve bu kimyasalların etki ettiği kontaminasyon tipi, Tablo 1’de görülmektedir.
Hassasiyet gerektiren katman depolama ve ısıl oksidasyon süreçleri için bazı durumlarda pul yüzeyindeki organik kirlilikler pirana çözeltisi ile (H2 SO4 :H2 O2) alınmaktadır. Depolama ve ısıl oksidasyon süreçlerinden ve bazı özel durumlarda şekillendirme süreçlerinden önce parçacık kaynaklı kir ve organik safsızlıklar, NH4 OH:H2 O2 :H2 O (SC-1) çözeltisi, pul yüzeyindeki metal kaynaklı kir ise HCl:H2 O2 :H2 O (SC-2) çözeltisi kullanılarak temizlenmektedir. RCA (Ratio Corporation of America) temizliği olarak da adlandırılan bu süreçler, megasonic banyo kullanılarak da gerçekleştirilebilmektedir. Megasonic temizlik işlemi, pullara minimum zarar veren hassas bir yöntem olduğu için yarıiletken sektöründe tercih edilen bir temizlik yöntemidir.
Kimyasal buhar depolama veya ısıl oksidasyon ile kaliteli bir silisyum dioksit (SiO2) depolamadan önce silisyum pulların son temizlik sürecine girmesi gerekmektedir. Ön temizliğin amacı silisyum pulların üstündeki doğal veya depolanmış ince SiO2 tabakalarını aşındırmaktır. Aşındırma işlemi seyreltik HF (1:100-1:200) banyolarında gerçekleştirilmekte ve SiO2 film oluşturma süreçlerine bu aşamadan sonra devam edilmektedir.
Aşındırma süreçlerinden sonra fotorezistin yüzeyden sökülmesi ve aşındırma reaksiyonları sonucu oluşan reaksiyon artıklarının uzaklaştırılması için de temizlik işlemleri yapılmaktadır. Pul yüzeyinden yalıtım kaynaklı malzemeler (SiO2, Si3 N4) veya poli-silisyum katmanı aşındırıldığında H2 SO4 :H2 O2 karışımı (Sulfuric acid- hydrogen Peroxide Mixture-SPM), metal bir katman aşındırıldığında ise ticari EKC ürünü temizlik amaçlı kullanılmaktadır. Bazı durumlarda seyreltik HF çözeltileri ile temizlik de gerçekleştirilebilmektedir.
Islak temizliğin yanı sıra YİTAL’de kuru temizlik işlemleri de yapılmaktadır. Kuru temizlik işlemleri plazma reaktörlerde gerçekleştirilir. Fotorezisti silmek ve aşındırma sonrası oluşan polimerleri uzaklaştırmak için O2, doğal oksidi uzaklaştırmak için ise NF3 gazı kullanılmaktadır. Tüm bu ıslak ve kuru temizlik süreçlerinden sonra pullar yıkanıp kurutulmaktadır.
Bakteriler, organik maddeler, iyonik kirlilikler ve partiküller gibi süreç suyundaki safsızlıklar transistör verimini düşürmektedir.
Pulların yıkanması için ultra saf su kullanılmaktadır. İnorganik veya organik çözücülerin kullanıldığı tüm ıslak temizlik adımlarında, yüzey reaksiyonlarını durdurmak ve yüzeyi yüksüzleştirmek için iyonize olmayan su ile son durulama yapılmaktadır. Silisyum dioksit, katkılı veya katkısız silisyum, nitrür veya poli-silisyum filmler gibi farklı yüzey yapıları, özellikle ıslak temizleme kimyasalları ve yüzeyi yüksüzleştirmek için deiyonize su ile etkileşime girmektedir.
Pulların yüzey koşullarına bağlı olarak durulama suyu ile teması için tanka daldırmalı temizlik, sprey temizliği, yüksek basınçlı püskürtme temizliği, sıcak temizlik gibi çeşitli teknikler kullanılmaktadır. Bir temizlik adımı başına toplam ultra saf su tüketiminin 5 ila 10 litre arasında olduğu tahmin edilmektedir. Bu, mikroelektronik devre üretiminde her bir pul için 1000-5000 litre arası su tüketildiğini ifade eder.
Saflığın İzlenmesi
Yarıiletken temizliği için kullanılan ultra saf suda istenmeyen safsızlıklar hâlâ bulunabilmektedir. Bu safsızlıklar, mikroorganizmalar, mikron altı parçacıklar, silika, iyonik kirleticiler, organik maddeler, çözünmüş oksijen ve benzeri maddelerdir.
Kirletici madde yoğunlukları ile transistör verimi arasında bağlantı mevcuttur. Bu yüzden, maliyetli bir üretim hattının su dağıtım sistemindeki kirlilik nedeniyle büyük miktarlardaki transistör üretiminde oluşabilecek zararları önlemek için safsızlık yoğunluğunun hassas bir şekilde izlenmesi gerekmektedir.
Temizlik hattındaki ve kullanım noktasındaki suyun kalitesini izlemek için bir dizi analitik teknik uygulanmaktadır.
İnorganiklerin İzlenmesi: İnorganikler genel olarak metalik safsızlıklar veya Na, Fe gibi belirli maddelerdir ve plazma spektroskopisi ile izlenmektedir. (Günümüz yarıiletken uygulamaları için kabul edilebilir metal yoğunlukları alt ppb aralığındadır. Bu seviye aşılırsa üretim derhal durdurulmalı ve Kontaminantları üretim alanından çıkarmak için sistem temizlenmelidir.) İnorganik kontaminasyon kapsamında olan iyonik safsızlıkların izlenmesi ise otomatik sıcaklık dengelemeli iletkenlik ölçer içeren direnç ölçümleri ile gerçekleştirmektedir.
Mikroorganizmalar ve organiklerin İzlenmesi: Canlı bakterilerin sayımı kültürleme yöntemlerine dayanmaktadır. Bu yöntemler, mevcut bakteri sayısıyla kabaca orantılı ölçüm sonuçları veren epifloresana ek olarak kullanılmaktadır. (Epifloresans ölçümleri, bir boyanın farklı bakteriler tarafından değişiklik gösterebilen alım miktarına dayanmaktadır.) Çok düşük seviyelerde organik parçacıkların izlenmesi gerekiyorsa pirojen testleri de kullanılabilmektedir. (Pirojen testleri tüm tesis genelinde değil, ultra filtreleme üniteleri gibi belirli noktalarda kullanılmaktadır.)
Bakteriler ve organik madde varlığı da kabul edilebilir sınırları aşarsa, sistemin temizlenmesi gerekir ve ek olarak dezenfekte işlemleri gerekli olabilmektedir. Mikrobiyal kirlenmeyi kontrol etmek için ozonlama yöntemi de kullanılabilmektedir.
Mikro parçacıkların İzlenmesi: Organik veya inorganik kaynaklı mikro parçacıklar He/Ne lazerleri kullanan bir optik ölçüm sistemi ile izlenmektedir. 0,3 ila 0,5 µm boyutlarındaki parçacıklar günümüz teknolojisi ile tespit edilebilmektedir. Parçacık sayılarını düşük tutmak için sistemin farklı noktalarında 0.1 µm filtreler kullanılmaktadır.
YİTAL’de Saf Su Üretimi ve Kullanımı
Günümüz ve gelecek için belirlenecek standartlara ulaşmak için tesis donanımı ve çalışma süreçlerine ek olarak, su arıtma sisteminin optimize edilmesi de çok önemlidir. Aşağıdaki şekilde, YİTAL deiyonize su üretim sistemi gösterilmiştir. Saf su içindeki safsızlık yoğunluklarını en aza indirmek için çeşitli filtreleme cihazları (Osmoz, 1 µm ve 0.03 µm filtreler), iyon değiştiriciler (aktif karbon, reçine ve karışık yatak iyon değiştirici) Ve mor ötesi ışınım (UV) kullanılmaktadır. Toplam organik karbon ve direnç ölçümleri ile anlık saf su takibi yapılmakta ve inorganik, organik ve parçacık analizleri gerçekleştirilmektedir. Toplam organik karbon değeri teknolojinin gerektirdiği gibi 1 ppb’nin altındadır.
Saflığından emin olunan su, temizlik sürecinin son aşamasında kullanılmak üzere pompa yardımıyla banyolara basılmaktadır. YİTAL su banyolarında, tümdevre temizliğinde kullanılan tanka daldırmalı temizlik, sprey temizliği, yüksek basınçlı püskürtme temizliği, sıcak temizlik gibi tekniklerin tümü uygulanmaktadır. Yıkama işlemleri, direnç 10 MΩ değerini geçene kadar yapılmaktadır.
Yıkama işlemi tamamlandıktan sonra, yüzey gerilimi prensibi (Marangoni Tekniği) ile çalışan kurutma cihazı yardımıyla veya sıcak azot üflemeli döner kurutucular ile pullar kurutulmaktadır.