Eklemeli imalat ve kafes yapılar ile tasarım
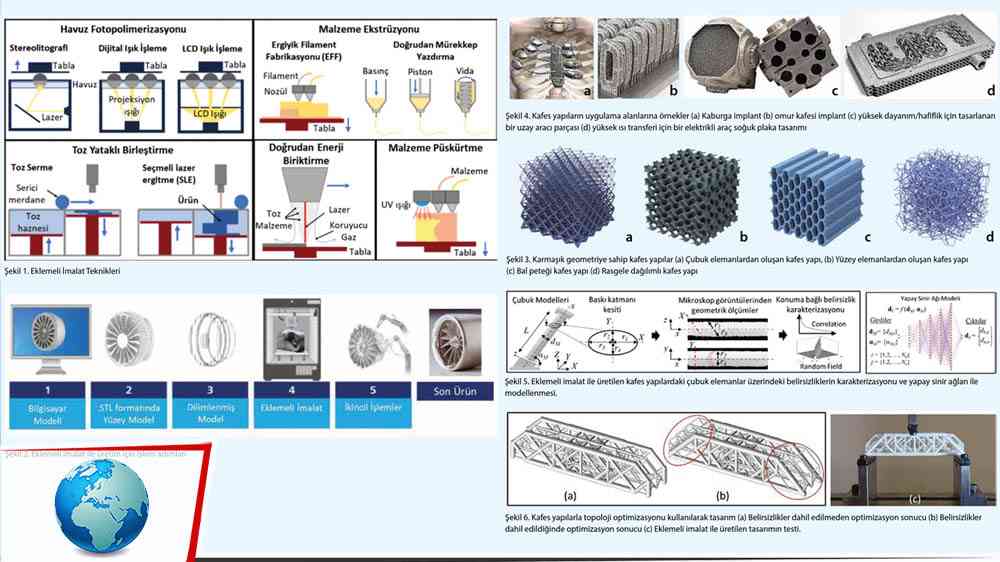
07/11/2022 16:26
07/11/2022 16:26
TOBB ETÜ Makine Mühendisliği Bölümü Öğretim Üyesi Dr. Recep Muhammet Görgülüarslan, Ekonomik Forum dergisi için kaleme aldı:
EKLEMELİ İMALAT VE KAFES YAPILAR İLE TASARIM
Eİ yöntemleri, dijital bir 3 boyutlu tasarım dosyasından farklı formdaki malzemeleri birbirine ve üst üste ekleme stratejisine dayanarak fiziksel bir obje yaratma teknolojisidir. Bu teknoloji, bilgisayar destekli tasarım verilerinden karmaşık 3 boyutlu nesneler üretme sürecini önemli ölçüde kolaylaştırır. Bu teknolojiyi geleneksel aşındırmalı imalat yöntemlerinden ayıran en temel özellik; üretim sürecinde blok bir malzemeden talaş kaldırmak yerine, çeşitli formlardaki malzemeleri katman katman birbirlerine ekleyerek ve bütünleştirerek üretimin tamamlanmasıdır. Malzemelerin katman katman yığılması stratejisi sayesinde, talaş kal dırma tekniğine dayanan geleneksel üretim yöntemleriyle üretilmesi zor veya imkânsız olan karmaşık geometriye sahip parçaların üretilmesi Eİ yöntemleri ile mümkün olur. Eİ yöntemlerinin sağladığı bu avantajlar, özellikle havacılık, otomotiv ve biyomedikal endüstrilerinde prototipleşmenin ötesinde karmaşık geometriye sahip, daha hafif ve dayanımı yüksek yapıların üretilmesini mümkün kıldığından, bu yöntemlere ilgi her geçen gün artmaya devam ediyor. Nispeten olgunlaşma sürecinde olan eklemeli imalat yöntemleri, sağladığı özgün avantajlar nedeniyle gerek akademik çalışmalar gerekse endüstriyel uygulamalarda çarpıcı bir gelişme elde etmiştir.
Eİ teknolojileri alanındaki gelişmeler
Eİ alanında ilk gelişmeler, uygulamada büyük kolaylıklar sağlaması nedeniyle hızlı prototipleme alanında gerçekleşmiştir. Bu alanda yapılan çalışmalar, 1950-60 dönemlerinden beri süregeliyor olsa da farklı Eİ teknikleri için patent başvuruları ve ticarileşme adımları 1980’lerin başlarından itibaren gerçekleşmiştir. Şekil 1’de, yaygın kullanılan Eİ teknikleri gösterilmiştir. 1987’de 3D Systems, havuz fotopolimerizasyonu tekniklerinden olan stereolitografi (SL) tekniği olarak bilinen plastik işleme yöntemini ilk kez ticarileştirerek endüstriyel uygulamalarda çözümler sağlamıştır. Bu yöntemde, ışığa duyarlı polimerler, bir lazer yardımıyla katman katman katılaştırılarak, özellikle mühendis ve tasarımcılara etkili prototip çözümleri sağlanmıştır. Polimer tabanlı Eİ teknolojileri, 1989’da Stratasys tarafından birleştirmeli yığma modellemesi (Fused Deposition Modeling, FDM) yönteminin patentinin alınması ve ticarileşmesiyle birlikte yaygınlaşmıştır.
Genel olarak malzeme ekstrüzyonu prensibine dayanan bu yöntemde, kalın ip (filament) halinde bulunan malzeme yüksek sıcaklıktaki bir nozülde eritilip istenilen bölgeye sürülerek, katılaşıyor. Her katmanda bu sürecin gerçekleştirilmesi ile nihai parça üretimi gerçekleşiyor. Bir filamentin eritilmesi prensibine dayandığı için bu yöntem, ergiyik filament fabrikasyonu (EFF) (fused filament fabrication, FFF) ismiyle de biliniyor ve düşük maliyetinden dolayı günümüzde bireysel hobi amaçlı kullanımlarda da tercih ediliyor. Malzeme ekstrüzyonu yöntemi sıvı halde bulunan malzemenin basınç, piston veya vida ile nozülden geçirilerek, yazdırılması süreci olan “Doğrudan Mürekkep Yazdırma” tekniği olarak da kullanılıyor. Bu teknik genelde biyomedikal alanda doku, organ ve hap basımı süreçlerinde tercih ediliyor.
Bir diğer Eİ tekniği ise toz halinde serilen malzemenin ile istenilen bölgelerde ergitilerek birleştirilmesi işlemine dayanan toz yataklı birleştirme yöntemidir. Bu yöntemlerden en yaygın kullanılanı, lazer ile ergitme işleminin yapıldığı, Seçmeli Lazer Sinterlemesi (Selective Laser Sintering, SLS) yöntemidir. SLS yöntemi de yine 1980’lerin sonunda geliştirilmiştir. Başlangıçta polimer malzemeler için kullanılan bu yöntem, 1994’te EOS firması tarafından metal tozları için de kullanıma başlanmıştır. Bu yüzden doğrudan metal tozu sinterlemesi (Direct Metal Laser Sintering, DMLS) veya Seçmeli Lazer Ergitme (SLE) (Selective Laser Melting) isimleri ile de tanımlanır. Bu süreçlerin yanında malzeme ve lazerin beraber yüzeye eklendiği “Doğrudan Enerji Biriktirme” yöntemi de genel olarak metal ile üretim için kullanılır. Bu yöntemde enerji ve malzeme dışarıdan püskürtüldüğü için, bir toz haznesine sahip olan toz yataklı birleştirme yöntemine göre daha büyük boyutlardaki parçaların üretimine imkân tanır. Benzer bir üretim tekniği ise sıvı haldeki malzemenin püskürtülmesi ve ultraviyole ışık ile katılaşması işlemine dayanan “Malzeme Püskürtme” işlemidir. Bu işlem ultraviyole ışık ile katılaşabilen polimerlerin üretiminde kullanılır. Farklı renk ve malzemelerin bir arada kullanımına imkân tanıması bu yöntemin avantajlarıdır.
Eklemeli imalat prosesinin temel işlem adımları nelerdir?
Üretim yöntemi fark etmeksizin eklemeli imalat prosesinin temel bazı işlem adımları mevcuttur. Masaüstü tipi 3 boyutlu yazıcılardan, büyük ölçekli endüstriyel Eİ cihazlarına kadar tüm üretim süreci bilgisayar modeliyle başlayarak devam eden birkaç adıma dayanır. Eklemeli imalat prosesinin temel adımları Şekil 2’de gösterilmiştir.
Şekil 2’de gösterilen adımlar aşağıda açıklanmıştır:
1) Bilgisayar destekli tasarım (BTM) modeli: Üretilecek parça geometrisini tamamıyla temsil edecek bilgisayar modelinin oluşturulması aşamasıdır.
2) Standart Triangle Language (STL) dosya formatına dönüştürme: Bilgisayar destekli tasarım modelinin yüzeyi üçgen çözüm ağı elemanları kullanılarak temsil edilmesidir.
3) STL modelinin dilimlenmesi ve yazdırma yolunun oluşturulması: STL formatına dönüştürülen parça modeli, ardışık iki nokta arasında katman kalınlığı kadar mesafe kalacak şekilde yatay dilimlere ayrıştırılır. Bu veri eklemeli imalat cihazına ait ekstrüzyon kafasının izleyeceği yığma yolunu belirler. Bu adımda, üretim parametreleri de ayarlanır. Üretimde kullanılacak malzeme, parçanın kullanılacağı uygulama ve eklemeli imalat yöntemine göre üretim parametrelerinin; katman kalınlığı, tarama genişliği, tarama tipi, yatak sıcaklığı, doluluk oranı vb. belirlenir. Dilimleme bilgileri ve üretim parametreleri G-kod dosya tipine aktarılır.
4) Eklemeli İmalat ile üretim: G-kod dosya tipi eklemeli imalat cihazına tanıtılır ve cihaz bu dosyadaki bilgilere göre üretime başlar. Parçanın oluşturulması otomatik bir süreçtir ve büyük ölçüde denetim olmadan devam edebilir. Üretim malzemesinin kontrolü, yazılım ve üretim hatalarını önlemek amacıyla üretim süreci görüntüleme uygulamalarıyla izlenebilir.
5) İkincil işlemler: Üretimin tamamlanmasının ardından nihai parça üretim tablası yüzeyinden alınması ve ikincil işlemler için hazırlanması aşamasıdır. İkincil işlemler, eklemeli imalat sürecinde kullanılan destek yapıları, üretim sürecinde oluşan kalıntı ve çapak gibi orijinal bilgisayar modeli geometrisi haricindeki malzemelerin parça yüzeyinden arındırılması işlemleridir. Hedeflenen mekanik özelliklerin sağlanabilmesi için uygulanan; ısıl, kimyasal ve metalografik işlemlerin tamamıdır.
6) Son ürün: Nihai bir model veya ürün oluşturmak için diğer mekanik veya elektronik bileşenlerle birlikte üretilen parçanın montajlanarak veya doğrudan çeşitli uygulamalarda kullanılmasıdır.
Karmaşık geometriye sahip yapıları doğrudan üretmesiyle önem kazandı
Eklemeli imalat, özellikle, talaş kaldırma veya döküm gibi geleneksel üretime teknikleri ile üretilemeyen, karmaşık geometriye sahip yapıları doğrudan üretebilmesi avantajı sayesinde önem kazanmıştır. Bu karmaşık geometriye sahip yapılardan en önemli olanları, atomların malzeme içerisindeki diziliminden ilham alınarak oluşturulan ve içinde boşluklar olduğu için hafif olmasına rağmen yüksek dayanım sağlayan kafes yapılardır. Şekil 3’te farklı türleri gösterilen kafes yapılar, birbirine bağlı karmaşık çubuk, plaka veya matematiksel yüzey ağı içeren milimetre veya daha küçük seviyelerde içyapılara sahip hücresel yapılar olarak bilinir. Eklemeli imalat yöntemlerindeki gelişmelerle birlikte üretimleri mümkün kılınan bu yapılar, ağırlık kısıtının önem arz ettiği uygulamalarda yaygın olarak tercih edilir. Kafes yapılar sayesinde, performans kaybı olmadan mevcut bir tasarımın ağırlığı yüzde 50 ve daha fazla azaltılarak, daha az malzeme kullanılarak, üretim maliyetlerini azalttığından eklemeli imalatı ekonomik hale getirebiliyor.
Biyomedikal alanda Şekil 4(a)’daki gibi kaburga ve omurga implantları, Şekil 4(b)’deki gibi omur kafesi implantlarında hafif tasarımlar elde edilebiliyor. Havacılık endüstrisinde hafiflik oldukça önemli olduğundan hava ve uzay araçlarının parçalarının hafifleştirilmesinde kullanılabiliyor. Örneğin, Şekil 4(c)’de gösterilen Aerojet Rocketdyne firmasının uzay aracı parçası, kafes yapıların kullanımı ve eklemeli imalat ile üretimi sayesinde yüzde 67 oranında hafileştirilmiş ve üretim maliyeti de yüzde 66 oranında azaltılmıştır. Yüksek dayanım yanında, yüksek ısı ve akış transferi uygulamalarında da kafe yapılı tasarımlar ön plana çıkmıştır. Örneğin, Şekil 4(d)’deki Puntozero firmasının elektrikli araç için tasarladığı soğuk plaka mevcut tasarımlara göre yüzde 25 daha hafif olup, yüzde 300 daha iyi ısı transferi gerçekleştirebiliyor.
Karakterize edilen belirsizlikler, yapay sinir ağları kullanılarak, bir yapay zeka modeli kuruluyor
Latis yapıların sağladığı avantajlara rağmen, eklemeli imalat yöntemleri kullanılarak, bu yapıların tasarım ve üretimi sırasında oluşan ve aşılması gereken bazı zorluklar bulunuyor. Birçok araştırma grubu bu zorluklar üzerinde çalışmalarına devam ediyor. Bu zorlukların başında eklemeli imalat ile üretim sırasında oluşan kusurların ve belirsizliklerin, geometri ve malzeme özelliklerinde değişimlere neden olması geliyor. Mikro ve milimetre seviyelerinde oluşan bu değişimler, makro seviyede tüm kafes yapının mekanik özelliklerini ve performansının güvenirliğini olumsuz yönde etkiliyor. Bu yüzden, kafes yapıları oluşturan elemanların üretim sürecinde yüzey ve kesit alanlarında oluşan değişimlerin tasarım ve analiz süreçlerine dâhil edilmesi gerekiyor. TOBB ETÜ’de bulunan alt yapı sayesinde, Şekil 5’te gösterildiği gibi eklemeli imalat ile üretilen kafes yapılardaki çubuk elemanların belirsizliklerin karakterizasyonu ile bilgisayar modellemeleri ve analizlerine dâhil edilmesi mümkün oluyor. Karakterize edilen belirsizliklerin bilgisayar modellemelerine dâhil edilmesi için yapay sinir ağları kullanılarak, bir yapay zeka modeli kuruluyor.
Şekil 5(b)’de gösterilen örnekte, yapay sinir ağı modeline girdi olarak karakterize edilen çubuk çap ve açılarındaki belirsizlikler veriliyor ve çıktı olarak modelle kullanılabilecek çaplar tahmin ediliyor. Yapay sinir ağı ile tahmin edilen çaplar, kafes yapıların topoloji optimizasyonu ile tasarımı sürecinde kullanılıyor. Şekil 6(a)’da belirsizliklerin düşünülmediği durumda Şekil 6(b)’de belirsizliklerin dâhil edildiği durumda kafes yapı ile topoloji optimizasyonu sürecinde elde edilen bir tasarım gösterilmiştir. Şekil 6(b)’de kırmızı ile gösterilen kısımlarda belirsizliklerin farklılıklar oluşturduğu gözlemlenmiştir. Şekil 6(c)’de ise bu tasarımın eklemeli imalat ile üretilmiş bir numunenin TOBB ETÜ laboratuvarlarında gerçekleştirilen testinden bir resim gösterilmiştir.